Park Collieries, 1948 to 1959
Seneley Green Drift

About this time, in 1949-50 the NCB decided to open up a drift mine in Seneley Green. This was in an area of land to the West of the colliery, in Arch Lane, Garswood and I was allowed to go there for some experience, as I was still in the colliery management course.
When I arrived, the contractors had just completed the two tunnels to the seam, which was the Wigan 5ft. They had done this by excavating the ground to expose the seam, and then constructing the tunnels in the cutting, using arches and mesh, covering the whole of the structure with a skin of concrete. The overburden was then backfilled to bury the tunnels, and the mining side of the operation started from there.
The men in charge were Bill Yates and Gordon Gittins, as fireman and shotfirer, respectively, and three more workmen, Bert Millett, Colin Banks and Jack Ratcliffe, joined them. There were more men in the return tunnel but I don't recall their names. The lamps for the men had to be brought and taken back each day by Arthur Wadsworth, the lampman at Stone's, who would hang the lamps on his pushbike!
The first job to be done was to drive pointed steel bars into the rock face at the crown of the arch to establish a bridgehead. We made a start on the Friday, but over the weekend it rained hard and washed a load of clay slurry into the tunnel, through the gap that we were attempting to cover. This had to be removed by use of a wheelbarrow, pulled up the slope of the drift by a rope and "donkey" i.e. me!!
We had a conveyor established to take out the spoil, and it delivered into a wagon. At first the coal seam was 4ft 6ins thick, and it wasn't too bad working, but later on it thinned down a lot. We managed to get under the solid top with an arch, and from then on it was straightforward pit work.
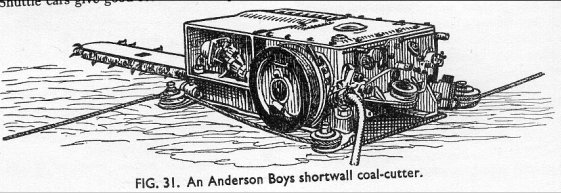
To cut the coal, a shortwall cutter was used, which was a machine with a 7ft jib, which undercut the coal. It had a rope drum on either side of it, and these ropes were taken round pulleys attached to the front of the machine. Holes were drilled in the floor, one on each side of the roadway, iron plugs inserted, and the ropes attached to these. When the operator started the machine, it pulled itself forward on the ropes until the jib was fully under the seam, and then by operating each rope drum in turn, he could cut across the full width of the heading.
The roadway was driven in the seam, supported by 7ft corrugated iron face bars and props. With the back ripping to 11x12x9 arches done later on. The roof of the mine was sandstone and the floor was fireclay, and this was a deadly combination, as I will explain. The drift was wet, as most drifts are, and we installed a Victor scraper to deliver to the belt return end. This was extended as the coal was mined. The Victor was the forerunner of the Panzer or armoured face conveyor (AFC) which is in use in all mines today. Where the AFC has a double chain running captive in two grooves, the Victor had a single central chain with flight bars on either side of it. If the trays of the Victor weren't graded exactly right, the chain rode out of them. When sandstone was being filled, the action of the water on the stone was like a grinding wheel, and soon the trays and chain were getting worn. Added to this, the fireclay from the floor would clog up and compact in the bottom of the tray where the chain returned. The fail-safe on the Victor was a set of shearing pins in the drive head, and when the bottoms of the trays were clogged up, the pins would shear off. We must have used dozens! When everything else failed, the final solution was to strip the conveyor down and physically remove the entire compacted fireclay from the bottom tray.
The roadway had been driven for about 50yds, down both the main tunnel and the return, when it was decided to drive a cross cut to connect the two. This was to take the fresh air base further in. Whilst we were making this, a bizarre incident occurred. It happened this way: we were using an air compressor to drive the air tools such as the jigger pick and the drilling machine. The compressor, a Broomwade petrol engined one, normally used for jobs on the highway, was situated on the surface. Up to now, the compressor had stood in the open, but it was decided to make a shed for it to keep it out of the weather.
No one had realized in the construction of the shed that the exhaust pipe was inside it, as was the inlet for the air supply. The result was that the exhaust gases were being compressed along with the air and sent underground. The cross-cut was driven through using a jigger pick, so, being closed in from the fresh air in the tunnel, those working in there were being slowly poisoned by carbon monoxide. We all were feeling a bit sick and dizzy. At first Bill Yates thought that it was the result of not having enough air in the cross cut, so he said to let some air blow in from the end of the air hose, Of course, this made things worse, not better! Finally someone realized that the exhaust was to blame so the pipe was extended out of the shed. Using the Broomwade for a compressed air supply wasn't the best of ideas really. For example, because the air reservoir was only small, when the conveyor was run, it would only go for a few yards and then it had to stop while the air built up again.
Work continued in both tunnels until a point was reached where a small face was formed out. The only problem was that the seam was getting progressively thinner, and it finally reached a point were it was uneconomic to continue any further. It was also a very wet mine and I remember that the cutterman had to go home during the shift to change his clothes as they were so wet!
The seam was so thin finally that the 15ins AB machine was too tall, and a Low Seam Sampson machine had to be brought in, and this was only 12ins in height. Senely Green was one of the NCB's abject failures, and it was declared unworkable, but not before we had a fatality. It happened like this. There was an electrician from Leigh, his first name was Albert, and I don't recall his second. He and his mate, a young apprentice called Albert Thompson, were working at the bottom of the tunnel at the time, hanging cables along the side of the roadway.
At the top of the drift, two men had loaded a belt return end on to a tram, ready to send it underground. The haulage rope was attached to the tram and the stop blocks opened up. As the tram went over the crown of the drift, the shackle became undone and the tram careered down the incline. The shackle was a "knock-off" style and the pin had come out.
The electrician leapt across the conveyor belt to avoid the runaway, leaving his apprentice in its path. Then fate took a hand in the proceedings. As the runaway tram approached the lad, who was rooted the spot, it de- railed and the belt return end flew from the tram and shot across the conveyor, pinning the electrician to the side of the roadway, injuring him fatally. There was the usual inquiry, which put the blame on the type of shackle being used. This was then outlawed and taken out of service.
Whilst this mine was being worked we had a few management trainees, who were sent there for experience, notably Bill Gleave, who went on to be a lecturer in mining, first at Wigan Tech and then at Stoke-on-Trent. John Taylor, who immigrated to the US, and David Morton who became a mine manager somewhere. There was a lot of public money wasted on the Senely green project, the NCB went ahead and built a screening plant, bagging plant, offices, lamproom, all of which had to be demolished, a complete white elephant. I heard it said at the time that the whole operation had cost three quarters of a million pounds, which in 1949 was a great deal of money. When you look at the site today it's hard to imagine that there ever was a mine there. It was said at the time that, had there been any workable coal there, it would have been taken years before by one of the licensed mines such as Lavins or Gaffneys, which were operating in the area.
Face Training
I was sent into No2 pit to start my face training, and spent 6 months there on the Yard mine face. The training was split into three sections, filling coal and setting supports, ripping and packing, and coal cutting. The other lads didn't do all this, they only learned the first part, but I was a management trainee, so I did all the lot. The men who were the training instructors for coal getting etc. were Tom McNamara, Fred Smith and Bert Selby and the trainees spent a month with each man. The first trainer only filled a standard "stint", as the trainee with him was under close personal supervision.
I started my training with Tom McNamara, who was a tall man and I often wondered how he managed to crouch down under the 2ft 9ins that we worked under in the Yard mine. Tom lived near the Delph Tavern in Tontine, and one of his sons, Tony, was also at Stone's. Tony told me a tale once about their house. Apparently, these houses were very old and had beamed ceilings. The boards were a bit warped and the bedroom floor was immediately above the living room. Tony and his brother, Joe were upstairs getting ready for bed and Joe wanted to relieve himself in the chamber pot. As he did so, he missed the pot and the resultant stream ran through the cracks in the boards, dripping into Tom's cup of tea on the table below!!
I arrived for work that day, suitably dressed in pit drawers, and kneepads, with the usual clogs to complete the picture. We clambered on to the face while the belt was stopped, and crawled to our "breyds" or "stints" as the allotted amount of coal was known.
The first job when the belt started up was to fill off the "scuftings". This was the small coal that the cutter left as it cut its way up the face. As this was being done, props were inserted under the cut to act as sprags, and these were placed at intervals between the shot holes which had been drilled on the previous day. "Spurn" props were also set against the face to stop the coal from "rating" off and falling into the working place. While this was being done, iron bars, which were retrieved the previous day from the pack area, were laid straight by the side of the conveyor.
This conveyor was a 20ins belt riding on sections of structure, latched together, the structure had a back plate to prevent the coal being thrown over into the waste. When all the "scuftings " had been cleaned up, the next job was to prepare for shotfiring. As I said previously, sprags were placed under the cut, and it was in between these that the small coal had to be cleaned out from underneath. When a collier had a trainee, they would prepare two shots so that they could both work without being in each other's way. We used flat no3 spades in the Yard mine, as the working height didn't allow for a spade with a lift in the handle.
When the shot was prepared, a shout of "Shot leeter" would go up. He would come with his shots made up ready in his waistcoat pocket, strictly illegal of course, but done for speed. The shot hole was stemmed with "green brick" that came to the pit for the purpose, but when no bricks were available, we used small coal or dust.
Usually, the weight of powder used was 12oz for each "breaking in "shot. Where two shots were being fired together, the shotfirer would couple them in sequence, again not a legal thing to do but a practical one. We would retreat along the face while the shots were fired, and on our return, get going with the spades to make an inroad into the pile of coal, making our way to the back of the cut. As soon as practical, the supports had to be set, as the Yard mine had a pretty fragile roof.
When enough coal had been cleared away, a bar was set. There was a knack to doing this as each iron bar was about 70lbs in weight. As soon as the ground was prepared, a bar was placed in position on the floor, a suitable prop found, and then the bar raised and held to the roof with one hand, elbow resting on knee, whilst the prop was hammered in place under the bar, using a 7lb hammer. This prop was a temporary one to hold the bar in place while two more were set, and these were placed, one at the end of the bar near the conveyor and the other at a distance of 6ft from it, this distance being gauged by a full stretch of the arms and a hand span! Surprisingly this method worked and kept the face in line.
There was about 6ins of dirt taken from the top of the seam to give a decent working height, and as the coal was filled, this dirt was put at one side for the packing shift to use. At Stone's it was known as "flamper", a name that was always a mystery to me. When all the blown down coal had been shifted, the collier and trainee prepared the next shot for firing. The roof bars were set at a distance of 2ft 9ins apart.
A trainee passed along from one trainer to the next, after a month's work, each succeeding trainer had a bit more coal to shift, so by the time that the last trainer was reached, the trainee was nearly shifting a full stint of coal. This was to prepare him for a place on a working coalface. When I started my training, Wilf Phillips and Fred King were doing theirs. The shotfirer was Martin Towey and the fireman, Jimmy Thornley.
After my time spent with the colliers, I was sent with the team of men on the return roadway to do some ripping and packing training. These were Tom Smith, Bill Winstaney and Bert Rabbitt. Whilst on this work I learned the art of forming a pack out, and building the walls with pieces of stone, just like a dry stone wall.
On each face the support system was the same. There was a main gate road where the conveyor delivered the coal, and a top and bottom road at either end of the face. There were also middle roads which were used to allow the colliers access to the face instead of having to crawl a long way.
When these roadways were advanced, the dirt that was produced from the excavation was packed on either side under the face. The main gate packs were 14yds long on either side of the roadway, and the top, bottom, and middle road packs were 10yds long. In between the roadway packs, along the face, were strip packs and wastes of 8yds and 5 yds respectively. The waste was known as the "goaf" or in some cases as "gob". At that time packs were paid for at the rate of 4shillings and a penny per yard (20pence decimal) and the wastes at 5shillings(25p) each, for drawing off. I.e. removing the supports to allow the roof to fall, thus providing material for packing.
A packer who put a 8yd pack on and drew off a 5yd waste each day was paid 8x4shillings+1penny=32shillings and 8pence+cost of living allowance of 4shillingsand 11pence, a grand total of 37/7d or in decimal £1.87p, thus in a week he drew £9.35.
Rippers were paid for the ground excavated at the rate of 5.38d per cu.ft.and they had to put 6yds of pack on either side, before they started to count the yds of pack to be paid for.
The supports in the main gate were 11x12x9 arches fitted with stilts to allow for settlement of the ground as the face advanced. These stilts were strapped into the web of the arch leg by means of hose straps put on using a special tool provided for the job.
The middle and return roadways were supported with "cockering" This consisted of a 10ft wooden bar to the roof in the centre of the road, held in place by pointed props set from the bar and wedged into the sides of the roadway. There were 6 props to each bar, in 2s opposed to each other. The effect was that of a fish backbone, and sometimes cockering was known as "herringbone".
I was shown how to set "breaker bars" on either side of the roadway, so that when the rip was fired, the sides would hold up and not spill over into the packing track. The drilling pattern was 2 holes across the bottom half, 2 holes in the middle and 1 at the top. Thus when it was fired the ground was cut in the shape of a triangle. Tom Smith was in charge of the rip, and he prepared it for firing. While he was doing this, Bill, Bert and I were forming the back wall of the pack out, and filling dirt from the waste into the pack area.
We had to take dirt from the waste otherwise we wouldn't have had enough to complete the pack. A self-prop was erected so that the iron bar could be retrieved; the pack was built up and filled, up to the next bar when the process was repeated, and so on until the roadway was reached. We were supposed to retrieve the bars complete with the props, but if the prop was stubborn, and wouldn't come easily, a sharp pick was used to to chop through it and it was thrown into the pack and buried.
The face advanced about 8yds in a week, so the men on the job got about £49 between them, giving each of them around £16. This was also about the amount paid to the colliers, and the cutterman. The average amount of coal filled by each collier was 17tons/day. Trainees were paid a "colliers day wage" of £1.50/day, which was the fallback rate paid to face workers when not on piecework.
When the "caunch" or ripping was fired, Bert started to cast the blown down dirt back to Bill who then threw it into the pack. Any large pieces were put on one side for building the walls, these were known as "builders". I helped in building the walls, or sometimes giving the other two a spell over with a spade.
When it was the day to erect the 10ft bar, which was every other day, all the team assisted. We came into the heading and lifted the flat-topped bar up to the roof. Tom then got a prop to use as a jackleg, and secure the bar into position, setting the jack on top of the pile of dirt. The pointed props were sawn to length and hammered into place. The jackleg removed and work carried on. It was a simple, cheap, and effective way of timbering a roadway, especially in the Yard mine where the roof and sides were sound. When a district finished, all the "cockering" was salvaged, for re-use in other districts.
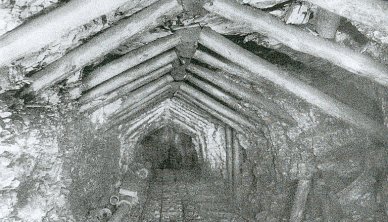
I had about a month working with Tom and Co and alternating with the coal cutting team. This was to keep me on the dayshift, as I was going to the Tech at the time on part time day release. The cutters worked days and nights alternatively, and the rippers were on days and afternoons. There were three men in the cutting team, Arthur Wadsworth, cutterman, Bob Boffey, second man, and Billy Corless, spragger. Arthur was an excellent cutterman, he could make an AB15 machine talk! He was one of four Wadsworths, all with the same Christian name, and all related, uncle, cousin and son. Stone's was a real family pit.
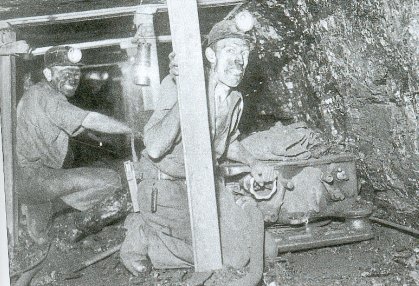
When we arrived at the face, the track cleaners were busy cleaning up in front of the machine, and then down the cutting track. The machine was in position for starting its journey down the face, having been turned round by the previous shift. Our first job was to change the picks in the jib. These, at that time were sharpened by the blacksmith and hardened in oil, and we had to pick them up on the surface before coming down the shaft. They looked for the entire world like a bird's beak, and were about 4ins long.
Arthur set these picks into their boxes on the cutter chain, using his forefinger as a gauge. Two joints was the length they were set at, and sometimes if he wanted to make the jib bite further into the floor, he would set some of the picks in the reverse position. As soon as the picks were in, the haulage rope on the cutter was taken round the face side of the machine and attached to a specially made bracket that could be fitted to the jib. Arthur then tightened the rope, put the pick race in gear and switched on.
It was a fearsome sight as the pick filled chain raced round the jib, and Arthur would start to give some more feed to the rope to pull the jib under the coal seam and gradually it disappeared from view. The cutter, while this operation was taking place, was spragged down to the floor by means of a couple wooden props, to hold it in place.
When the jib was fully home a locking pin was placed in position, the rope, now with its "D" link attached was re-routed down the face where it was anchored by means of a "spurn" prop, placed inside the "D"link. The tool used for making the "pitcher" hole to hold the prop in position was known as a "hawk", and was a hand pick, modified so that it had a hammer end and a point. The pick blade had one point cropped off and a big nut welded on to it to form the hammer head.
Bob gave a shout to Arthur to "tighten up" and Arthur would start to move the machine along the face, stopping after a couple of yards so that the "gummer", a contrivance for removing the "scuftings", could be fitted. This looked like a bottomless bucket with a propeller blade inside it, attached to the machine by a couple of turnbuckles and driven by a rotating "dog" at the end of the machine.
As the cutter made its way along the face, the small coal from the cut was deposited in a pile behind it. Billy Corless, the third man of the team had to crawl along, over this small coal, inserting props under the cut coal. I always thought that Billy had the worst and most poorly paid job of the lot. He was only paid colliers day wage, whereas Arthur got paid from the colliers "pool" and Bob got daywage plus a third.
At that time the colliers were paid around 9s/6dper ton (45p) and filled an average of 17-18 tons a day per man. Each collier had a stint or "breyd" of 7.5yds, the undercut was 4ft 6ins deep, and the coal seam was 2ft 3ins thick the weekly wage was round about £16-17 per man.
As the cutter moved forward, Arthur kept his eye on the colour of the scuftings. As long as he could see a fleck of grey in them, he knew that the jib was just on the bottom of the seam. To keep it there, he carried a wooden wedge to scrape together any small coal, and this was pushed under the outside edge of the machine to keep it tilted just right. I've seen him also use bits of wood as well.
As the machine made its way down the face, Bob took the slack cable into the middle road, the cable being in two halves, with a coupling box, and here the top half could be uncoupled and left until the next cutting shift.
The worst part of the cutting operation and the most dangerous was as the machine crossed the main gate heading, here the coal and the roof above it had to be spragged for the machine cut across it. Above the Yard mine seam about 4ft6ins up was a small band of coal 9ins thick. Above this small seam was a good, strong roof and it was to this roof that 10ft wooden bars were set to support the roadway in the main gate road. Between this seam and the main seam, the strata was a mixture of coal and dirt bands, which wasn't very strong, and it was under this that the colliers had to work and set supports, and it was for this reason that no more than 2shots could be fired together. The roof was said to be a bit "nesh". In the main gate, however, all this strata was exposed and it had to be watched very carefully as the cutter went through.
This piece of coal was usually worked and filled out by the face chargeman or "bummer" as he was known, and his mate, who took 5yds apiece across the front of the road and about a yard under each side. The chargeman's job was to make sure that the face was cleared of coal each shift, and by having less than anyone else to fill, if anyone had bad roof conditions, he would go and help them out. He also had to measure off the stints for the men.
To remove the coal in the gateroad, sprags were set under the raw edge of the ripping and just the thickness of the coal removed, setting self-props underneath to hold up the roof. There was no need to remove any more as each day the overburden was fired down and used for packing material, leaving a straight face of strata. While I was training, the main gate was supported on 10ft bars, with a back ripping a number of yards away, being carried out by another team of men, who put up arches. Later on, however, the whole operation was combined with a system of RSJs and chocks, so that one team, who fired both front and back rippings, could carry it out and set arches also.
Continued...